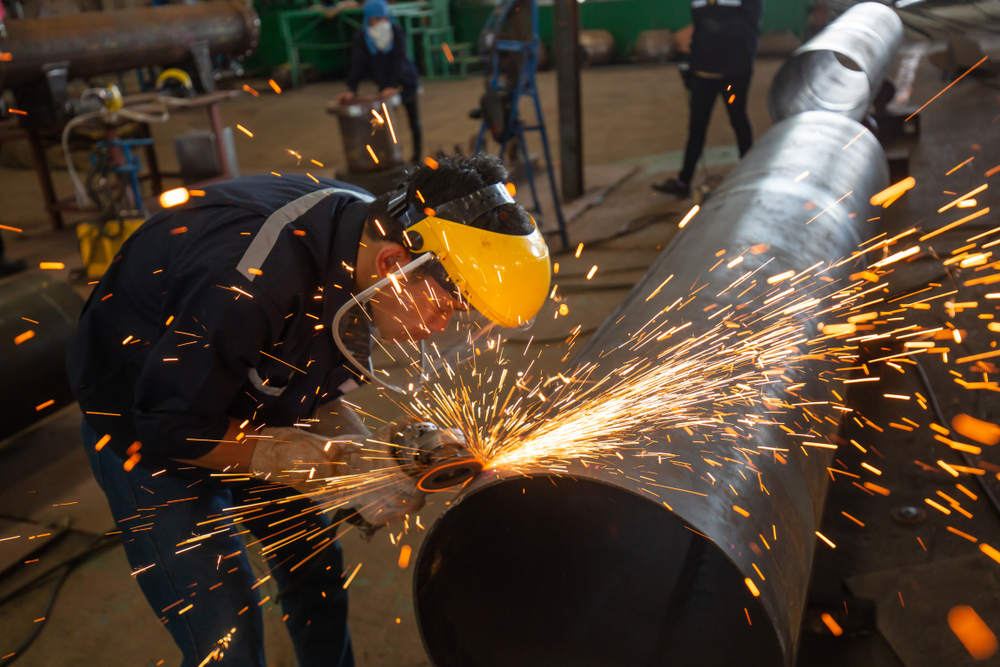
Steel fabrication and installation are critical components in the construction industry, playing a pivotal role in building structures ranging from residential homes to towering skyscrapers. While the end product—strong, durable steel structures—may seem like the focus, the process that brings these materials to life involves various safety risks. Ensuring that safety standards are followed in steel fabrication and installation is not just a matter of regulatory compliance; it’s about protecting the workers and the long-term integrity of the project. In this blog, we will explore the importance of safety in steel fabrication, the role of OSHA steel fabrication guidelines, welding safety standards, and the best practices for ensuring safe steel installation.
The Steel Fabrication Process
Steel fabrication is a meticulous process involving cutting, welding, bending, and assembling steel to create custom structural elements used in construction projects. The complexity of steel fabrication comes from its requirement for high-precision work, often involving the use of heavy machinery, high temperatures, and various hazardous tools. Workers in this field are exposed to a range of potential dangers, including burns, cuts, falls, and the risks associated with heavy equipment.
Steel fabrication typically begins in a controlled workshop environment where raw materials are shaped and prepared for installation. In this environment, workers are tasked with reading detailed blueprints, measuring and cutting steel beams, welding materials together, and ensuring that the structures meet the necessary design specifications. The fabrication process can be physically demanding and requires a high degree of skill and attention to detail. However, despite the intricacies involved in the work, the safety of the workers must always be the top priority.
The Role of OSHA Steel Fabrication Standards
The Occupational Safety and Health Administration (OSHA) plays a crucial role in regulating the safety standards of steel fabrication and installation. OSHA steel fabrication guidelines outline a set of rules that employers must follow to ensure the health and safety of their workers. These standards are designed to minimize the risk of accidents and injuries while maintaining an efficient workflow.
OSHA regulations cover every aspect of the steel fabrication process, from proper machine operation to the safe handling of raw materials. For example, when it comes to welding, OSHA mandates that workers wear appropriate personal protective equipment (PPE), including welding helmets, gloves, and flame-resistant clothing, to shield them from the intense heat and sparks produced during welding. OSHA also enforces guidelines for ventilation in spaces where welding takes place, as the fumes generated by the process can be toxic if inhaled.
Additionally, OSHA standards govern the safe use of overhead cranes, lifting equipment, and hoists, which are commonly used in steel fabrication. These devices are integral to transporting heavy steel beams and materials, but they also present significant risks if not properly maintained or operated. The training of workers to safely use these tools and the proper inspection of equipment are key components of OSHA compliance in the steel fabrication industry.
Incorporating these standards not only helps ensure worker safety but also improves the overall quality of the project. A workplace that adheres to safety protocols can avoid costly delays, prevent damage to materials, and reduce the likelihood of workplace accidents.
Welding Safety Standards in Steel Fabrication
Welding is one of the most integral components of steel fabrication. It involves joining two pieces of metal by applying intense heat, often with the help of additional filler materials. While welding is a skill that requires both knowledge and experience, it also introduces a variety of safety hazards. The extreme heat, intense light, and potentially harmful fumes make welding a high-risk activity for workers.
The primary welding safety standards focus on personal protective equipment (PPE), proper ventilation, and the prevention of fire hazards. Welding helmets with appropriate eye protection are essential to guard against the intense light and UV radiation emitted during welding. Additionally, workers are required to wear flame-resistant gloves and clothing to protect themselves from the risk of burns. In some cases, welding jackets or aprons may be used for additional protection.
Ventilation is another critical safety concern during welding operations. Steel fabrication shops often use various types of welding techniques, each generating different levels of smoke and fumes. These fumes can be hazardous to a worker’s respiratory health if inhaled over extended periods. Proper ventilation systems, such as exhaust fans and fume extractors, are necessary to ensure the air quality in the workspace remains safe. OSHA guidelines recommend that employers conduct regular air quality assessments to ensure that levels of hazardous fumes, such as manganese, chromium, and nickel, do not exceed permissible exposure limits (PELs).
Furthermore, fire safety is an important consideration when welding. Since welding involves an open flame, it’s essential to implement fire safety practices to prevent the risk of sparks igniting flammable materials. Steel fabrication workshops should have fire extinguishers readily available, and workers should be trained in how to respond to fires should one occur.
By adhering to welding safety standards, fabricators can ensure their workers remain safe while executing high-quality welds that are both strong and precise.
Steel Installation Safety Guidelines
Once steel elements are fabricated, they must be transported to the construction site and installed, a process that carries its own set of safety concerns. Steel installation often takes place at significant heights, with workers using scaffolding, ladders, and cranes to position and secure steel beams and structural components. This is one of the most dangerous phases of the project, as workers are exposed to fall hazards, moving machinery, and heavy materials.
One of the primary steel installation safety guidelines is fall protection. Workers who are working at heights of six feet or more are required by OSHA to wear fall arrest systems, such as harnesses, lanyards, and lifelines, to prevent serious injuries in case of a fall. Proper training on how to use fall protection systems and inspect their components is essential for ensuring worker safety.
Additionally, steel installers must be trained in the proper rigging techniques when using cranes and hoists to move steel beams. Rigging involves the use of ropes, chains, and slings to secure loads for lifting. Ensuring the rigging equipment is in good condition and that the load is properly balanced can help prevent accidents caused by dropped loads or unbalanced equipment.
Another critical aspect of steel installation safety is ensuring that workers understand how to safely navigate the construction site. Steel construction sites can be cluttered and chaotic, with various materials, tools, and equipment present. Clear pathways and signs, along with a culture of workplace safety, can help prevent accidents by ensuring that workers stay aware of their surroundings and follow safety procedures.
Promoting a Culture of Safety in Steel Fabrication and Installation
Safety is not simply about following guidelines and meeting regulatory standards; it is about fostering a culture of safety within the workplace. Employers in the steel fabrication and installation industry must make safety a top priority, ensuring that their workers are not only trained in safety protocols but also actively encouraged to practice them. This culture of safety should permeate every aspect of the job, from the design and planning phases to the actual hands-on work.
Regular safety training sessions are essential for reinforcing safety practices and keeping workers up to date on the latest safety standards. These training sessions should include both theoretical education about hazards and practical, hands-on experience in using safety equipment. Encouraging workers to speak up about potential hazards and report safety issues without fear of reprisal can also help create a safer work environment.
The role of supervisors is also crucial in promoting safety. Supervisors must lead by example, ensuring that they consistently adhere to safety standards and actively monitor their teams for compliance. Additionally, regular safety audits and inspections can help identify potential risks before they lead to accidents.
By creating a culture of safety, steel fabrication and installation companies can reduce workplace injuries, improve the overall quality of their work, and protect the well-being of their workers.
Conclusion
Safety in steel fabrication and installation is a multifaceted issue that requires ongoing attention and dedication. Adhering to OSHA steel fabrication guidelines, implementing welding safety standards, and following steel installation safety practices can significantly reduce the risks associated with these high-risk processes. More importantly, by promoting a culture of safety within the workplace, employers can ensure that their teams work in environments that prioritize their well-being, productivity, and success.
Need a Steel Fabricator & Welding Shop In Visalia, CA?
Suburban Pipe & Steel, Inc. DBA Flint Construction. in Visalia, California, doing business as Flint Construction, has been family owned since 1957. We truly understand steel buildings. We design, fabricate, and install all phases of pipe and steel structures for every industry. Contact us today to find out more about our services, rates, and to schedule a consultation. You can even fax us your drawings so we can have a better idea of your vision. We look forward to exceeding your expectations.